CNC A2
After almost missing an exam because my phone was a bit misaligned on its wireless charger, I decided I needed to fix it. The logical thing to do might have been to plug in the phone but I took a more extreme route.
When I had my longboard company I had built a CNC router. I didn't have any space for the machine so I designed a bench top version with the parts from the old machine.

The goal with the machine was to be able to prototype most common materials at home. I didn't want a freestanding machine so it had to fit on a normal bench top. My last goal was that the machine should have a workable area no smaller than an A2 paper, hence the name.
Features

Large work volume
Expendable height, max 210 mm for low force tasks.
Powerful stepper motors
Provide 500N even at 5000 mm/min.

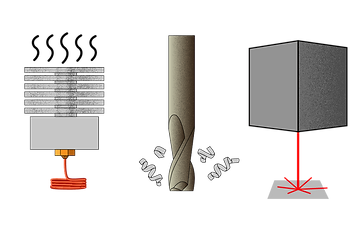
Swappable tool
Made for milling but can also do 3D printing, laser etching, pen plotting, and vinyl cutting.
Single X stepper
Minimizes the risks of misalignment or missed steps.

Specifications:
Build volume: 295 x 195 x 200 mm 11.61 x 7.67 x 8.27 in (W x D x H)
Rapid speed: 5000 mm/min 197 ipm
Cutting speed: up to 2400 mm/min 94 ipm
Mech resolution Z-axis: 8µm
Mech resolution X Y-axis: 24µm
Motion: 8.2Nm Nema 34 stepper motors
Control: External PC with parallel port
Spindle: Water-cooled 1.5kW 6K-24k RPM
Collet: ER11 (1-8mm)
Total machine power: 3600W
Bench footprint: 1050 x 610 x 720 mm 41.33 x 24.02 x 28.35 in (W x D x H)
Machine weight: ~70kg
Renderings
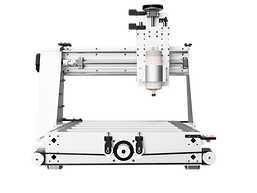


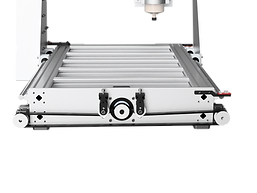
Pictures
CAD model
A 3D CAD model should be seen below. The files are shared under the Creative Commons Attribution-ShareAlike 4.0 International License.
You can find the 3D printed parts as well as a BOM here: CNC A2 files.
Tools I used
01/
CAD design
Originally modeled in SolidWorks. The CAD file contains more than 450 pieces (about 73 individual parts).
02/
Machine construction
This is one of my most advanced machines. It utilizes aluminum extrusions, ballscrews, linear rails, and timed belts.
03/
Electrical wiring
The machine has five different power systems (six if you count the VFD). The wiring is separated to minimize disturbance.
Things I learnt
01/
CAM
Even though I had learnt a lot from my first machine I never really got into 3D CAM. With the second version of the machine the I've been doing mostly 3D CAM.
02/
Workholding
As any CNC machinist would tell you, workholding is everything. I made my own 3D printed vises and have been playing around with 3D printed softjaws.
Here's a film of the phone charger I made. The original reason for rebuilding the machine.
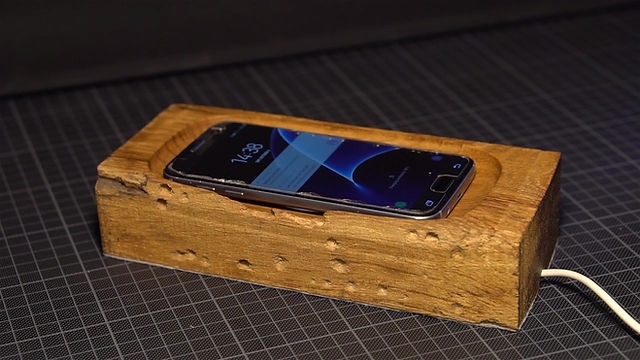